ZF’s Transformational Journey
HIGH-VOLUME, 5 S-COMPLIANT, SEMI-AUTOMATED LINE
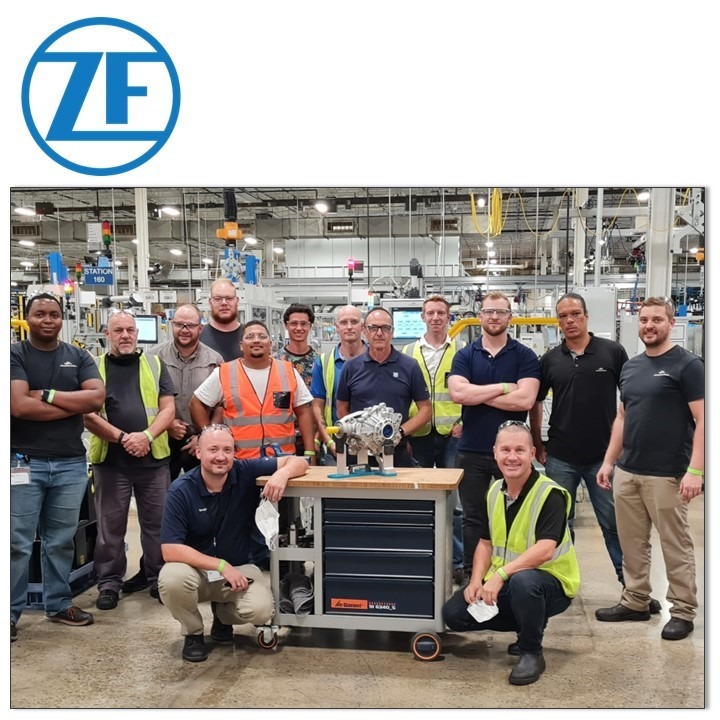
IMPACT
- Agile multi-variant production
- Reduced operator training times
- More organised and productive workspaces
sec Takt time
full auto stations
manual stations
The Customer Journey
About The Customer
ZF Friedrichshafen AG, a prominent global, tier-one
manufacturer, was founded in 1915 in Friedrichshafen,
Germany. The company gained prominence with innovations like the synchro-mesh transmission in the 1950s and developed pioneering technologies such as the first fully automatic transmission for passenger cars in the 1960s.
Since then, ZF has expanded worldwide, and diversified its product range to include powertrain components and steering systems, and made significant strides in electric and hybrid vehicle technology. The company also prioritised research and development into autonomous driving, advancing sensors and control systems. ZF remains a major force in the automotive component manufacturing sector, driving innovation within this ever-evolving landscape.

Cleaning it up
ZF has a long-standing customer relationship with Jendamark, ordering multiple semi-automated, automated and hybrid assembly lines for differential assemblies over time. Because of the stringent steps required to assemble differentials, along with concerns over high staff turnover and unavailability of skilled operators, ZF’s plant in Gainesville, USA, opted to integrate ODIN Workstation into its line as the operational software, to expedite onboarding and mitigate risk.

As such, everything needed to be standardised, simple to train on and use, while being flexible enough to make changes, additions, or updates, and easily add new variants to the models being assembled on the line.
First Prize
Whether a line is manual, automated, or semiautomated, ODIN Workstation acts as the lifeline between operator, software, and hardware at every station. When the operator receives their set of work instructions from ODIN Workstation, so do the tools and other hardware in the station. If, for example, the operator was to attempt to complete a bolting operation on the bolt not specified, the tool simply will not work, ensuring complete process security. ODIN Workstation’s easy-to-navigate interface facilitates on-the-job training for new operators, with the visual elements and presentation of assembly instructions easily guiding operators through even the most complex assembly steps. In this way, new differential variants are also seamlessly integrated.

Benefits
ZF has also benefitted from comprehensive reporting features, part and operator traceability, and the meticulous tracking and documentation of each component’s journey throughout the assembly process. This culminated in comprehensive quality assurance reporting, thereby underscoring both ZF’s and ODIN Manufacturing’s commitment to product excellence.
Now, all new operators first work on the lines with ODIN Workstation, and once they have a better understanding and improved performance, only then are they assigned to other positions within the plant.

Lean into it
In addition to the benefits already described, the customer later mentioned the need to incorporate Six Sigma and lean practices into their everyday business operations as part of the drive to remain current within the ever-changing manufacturing space. Though lean manufacturing principles offered logical advantages, their implementation had been impeded by administrative complexities. The procedural burden of managing paperwork for the 5S lean methodology and data collection proved time-consuming and labour-intensive.
A transformative 5S solution was introduced to optimise production line efficiency. This approach has helped to better instil good 5S practices among the operators, promoting a cleaner and more organised work environment. ODIN Workstation’s interface facilitated this by presenting 5S checks each morning before the start of the shift. Operators acknowledge completion of their cleaning activities, and those on the next shift can assess the preceding operator’s tidiness, while fostering a culture of responsibility.
ODIN Manufacturing’s intervention bolstered engagement and adoption of 5S principles on the ODIN Workstation-guided production lines, as the understanding of the value of 5S was markedly higher when compared to lines not running the software. It has also markedly reduced the workload of supervisors, who now benefit from automated reporting procedures instead of manual data compilation and report generation.

Facing staff turnover challenges, ZF needed to get operators up to speed fast in handling multiple variants, with ODIN Workstation software providing the bridge between operator, machine and work instructions.
Conclusion
This collaboration with ZF yielded significant advancements, notably addressing workforce turnover challenges, seamless integration of new product variants, meticulous data traceability, and the successful adoption of lean manufacturing principles. This transformative initiative not only optimised operations but also elevated overall efficiency and employee engagement across ZF’s production landscape.